The 5 Whys Analysis: Uncovering Root Causes for Effective Problem-Solving
- Nam H Le
- Aug 29, 2024
- 3 min read
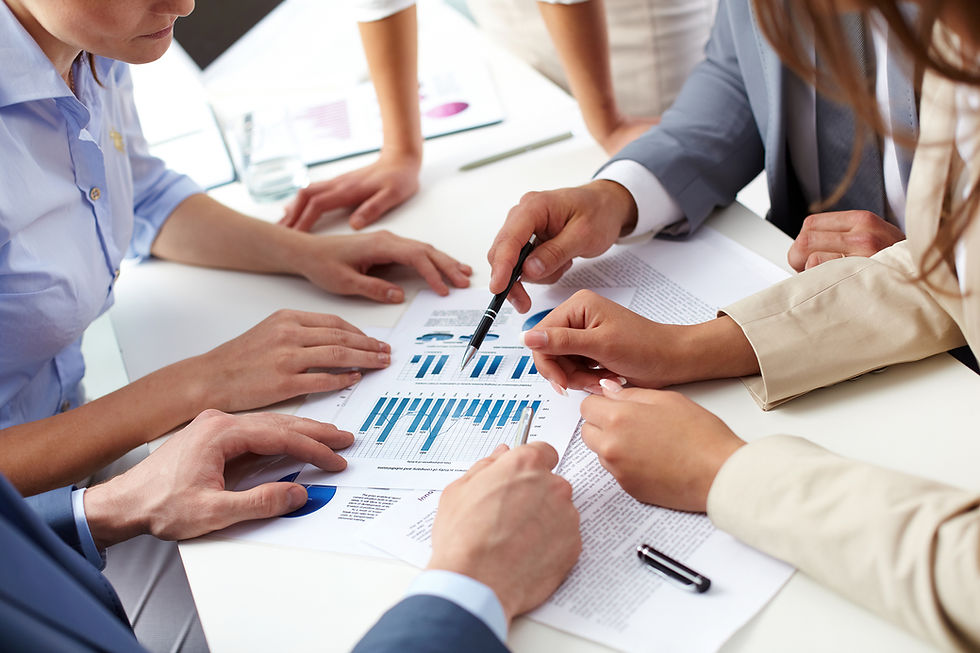
The 5 Whys analysis is a powerful yet simple problem-solving technique that has revolutionized how organizations approach root cause analysis. Developed by Sakichi Toyoda, the founder of Toyota Industries, this method has become an integral part of lean manufacturing and quality management practices worldwide.
Understanding the 5 Whys Analysis
At its core, the 5 Whys analysis is an iterative interrogative technique used to explore cause-and-effect relationships underlying a particular problem. The primary goal is to determine the root cause of a defect or problem by repeatedly asking the question "Why?" typically five times, though the number can vary based on the complexity of the issue.
How to Conduct a 5 Whys Analysis
Clearly define the problem statement
Ask "Why?" the problem occurred and document the answer
For each answer, ask "Why?" again
Continue this process until you reach the root cause
Verify that removing the root cause would prevent the problem from recurring
Benefits of Using the 5 Whys
Implementing the 5 Whys analysis offers several advantages:
Simplicity: Easy to learn and apply without complex statistical analysis
Flexibility: Can be used for a wide range of problems across various industries
Team engagement: Encourages participation and collaboration in problem-solving
Quick results: Often leads to actionable insights in a short time frame
Cost-effective: Requires no special tools or extensive training
Applications Across Industries
While originally developed for manufacturing, the 5 Whys has found applications in various sectors:
Software development: Debugging complex issues
Healthcare: Analyzing patient safety incidents
Customer service: Addressing recurring customer complaints
Project management: Identifying causes of project delays or failures
Best Practices for Effective 5 Whys Analysis
To maximize the benefits of this technique:
Involve the right people: Include those with direct knowledge of the process
Be specific: Avoid vague problem statements or answers
Focus on processes, not people: Aim to improve systems rather than assign blame
Document the process: Keep a clear record of each "why" and its answer
Verify root causes: Ensure that addressing the final "why" would prevent recurrence
Integrating 5 Whys with Other Tools
The 5 Whys analysis can be combined with other problem-solving tools for more comprehensive results:
Fishbone diagrams: Use 5 Whys to explore each cause identified in the diagram
Pareto analysis: Apply 5 Whys to the most significant issues identified
FMEA (Failure Mode and Effects Analysis): Use 5 Whys to delve deeper into potential failure modes
Limitations and Considerations
While powerful, the 5 Whys technique has some limitations to consider:
Subjectivity: Different teams might reach different root causes for the same problem
Oversimplification: Complex issues may require more than five "whys"
Linear thinking: May not capture multiple contributing factors effectively
To address these limitations, consider using the 5 Whys as part of a broader problem-solving approach, combining it with other analytical tools and methods.
Conclusion
The 5 Whys analysis stands as a testament to the power of simplicity in problem-solving. By encouraging deep, critical thinking about the causes of problems, this technique enables organizations to address issues at their core rather than merely treating symptoms. As businesses continue to face complex challenges, mastering the 5 Whys analysis can provide a valuable edge in maintaining efficiency, quality, and continuous improvement. Whether you're troubleshooting production defects, improving customer satisfaction, or optimizing business processes, the 5 Whys offers a systematic method to uncover root causes. By embracing this technique and integrating it with other quality management tools, organizations can enhance their problem-solving capabilities and foster a culture of continuous improvement.
Comments