Fishbone Analysis: Unraveling Complex Problems with Precision
- Nam H Le
- Aug 29, 2024
- 2 min read
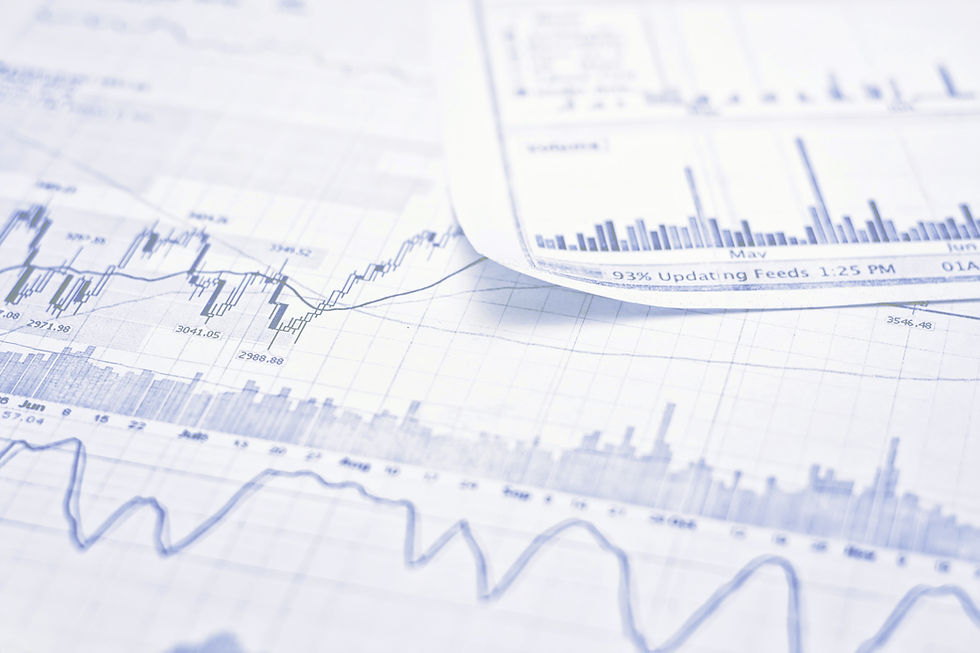
Fishbone analysis, also known as the Ishikawa diagram or cause-and-effect diagram, is a powerful visual tool used in root cause analysis and quality management. Developed by Kaoru Ishikawa in the 1960s, this technique has become an essential component of problem-solving methodologies across various industries.
Understanding Fishbone Analysis
The fishbone diagram gets its name from its distinctive shape, resembling a fish skeleton. The problem or effect being analyzed is placed at the "head" of the fish, while potential causes are listed along the "bones" branching off the central spine. This visual representation allows teams to systematically explore and categorize the various factors that might contribute to a problem.
Key Components of a Fishbone Diagram
Problem Statement: Clearly defined at the fish's head
Major Categories: Typically represented by the main bones
Potential Causes: Listed as smaller bones branching off the main categories
Common Categories in Fishbone Analysis
While categories can be customized based on the specific context, the most commonly used set is known as the "6 Ms":
Man (People)
Machine
Method
Material
Measurement
Mother Nature (Environment)
These categories provide a comprehensive framework for examining potential causes across different aspects of a process or system.
Creating a Fishbone Diagram
To construct an effective fishbone diagram:
Define the problem clearly
Draw the spine and add the problem statement at the head
Identify major categories and add them as main bones
Brainstorm potential causes within each category
Add sub-causes as smaller bones where applicable
Analyze the completed diagram to identify root causes
Benefits of Fishbone Analysis
Implementing fishbone analysis offers several advantages:
Provides a structured approach to problem-solving
Encourages team collaboration and diverse perspectives
Helps identify root causes rather than symptoms
Visualizes complex problems in an easy-to-understand format
Supports comprehensive analysis by considering multiple factors
Integrating Fishbone Analysis with Other Tools
Fishbone analysis is often used in conjunction with other quality management and problem-solving techniques:
5 Whys: To drill down into specific causes identified in the fishbone diagram
Pareto Analysis: To prioritize the most significant causes for action
FMEA (Failure Mode and Effects Analysis): To assess risks associated with identified causes
Applications Across Industries
While originally developed for manufacturing, fishbone analysis has found applications in various sectors:
Healthcare: Analyzing patient safety incidents
Software Development: Troubleshooting complex bugs
Business Management: Addressing operational inefficiencies
Education: Examining factors affecting student performance
Best Practices for Effective Fishbone Analysis
To maximize the benefits of this technique:
Involve a diverse team with relevant expertise
Focus on facts rather than opinions
Be specific when describing causes
Use the diagram as a starting point for further investigation
Regularly review and update the diagram as new information emerges
Conclusion
Fishbone analysis stands as a versatile and powerful tool in the arsenal of problem-solvers and quality management professionals. By providing a structured, visual approach to identifying root causes, it enables organizations to address complex issues more effectively. As businesses continue to face increasingly intricate challenges, mastering techniques like fishbone analysis becomes crucial for maintaining competitiveness and driving continuous improvement. Whether you're troubleshooting production defects, improving customer satisfaction, or optimizing business processes, fishbone analysis offers a systematic method to unravel the underlying causes of problems. By embracing this technique and integrating it with other quality management tools, organizations can enhance their problem-solving capabilities and foster a culture of continuous improvement.
Comments